Increasingly, manufacturers have turned to automation to overcome the difficult labor market. Most executives already know that streamlining operations is important. According to an MIT Sloan survey, executives at 91% of companies say digital technologies have the potential to fundamentally transform the way companies work.
The manufacturing landscape is changing
Driven by advances in artificial intelligence, robotics, the Internet of Things and other technologies, the benefits of the current industrial revolution are quickly becoming indispensable to modern life. Global provider of market intelligence, IDC, predicts that by 2021, 40 percent of manufacturers will have made a full, factory-wide digital makeover. And by 2022, 35 percent of manufacturers will have an entirely new digital ecosystem that includes more AI, robotics, and blockchain technology.
For the average American manufacturer, the benefits of automation can be a dramatic game-changer. In addition to solving the current labor shortage, robots create efficiencies, can be programmed for continuous production, are highly flexible, customizable, and can be cost-effective for nearly every size of company, including small shops.
Automation is becoming more affordable as it becomes more commonplace. However, funding the initial investment is still one of the biggest challenges for many manufacturers. In my experience speaking with manufacturing clients, it is not uncommon for leaders to be hesitant due to perceived high cost of scaling or concerns over justifying investment costs.
Depending on the extent and type of automation, a significant amount of upfront work may be needed. However, the cost-benefit is typically in favor of the manufacturer because automation typically leads to more efficient processes, shortened cycle times and down times, improved product quality, reduced energy losses, and better workplace safety.
Funding automation through local, state and federal levels
Furthermore, many manufacturers do not realize that there are readily available grants and credit programs, offered through cities, states and the federal government. These programs provide valuable seed funding for expansion and efficiency projects through automation on a national level:
Federal R&D Tax Credits help offset development and implementation costs for automation systems and provide a source of capital for the acquisition of technical talent. For instance, the PATH Act of 2015 makes R&D tax credit permanent and eliminates alternative minimum tax for small businesses.
The Manufacturing Extension Partnership National Network is a private-public partnership that assists manufacturing companies with development, expansion, and new technology. With centers located in all 50 states including Enterprise Minnesota and Impact Dakota, the network has a national supply of resources. Due to their local presence, MEP has deep knowledge of the local problems facing manufacturers.
There are also tax credits and grants available for manufactures to utilize at the state level:
North Dakota recently renewed its ND Automation Tax credit that allows manufacturers a credit of up to 20% of costs of equipment and technology used to automate a manufacturing process, as well as a tax credit that allows companies to exempt equipment from sales taxes for a new or existing plant. Similarly, South Dakota offers a reinvestment payment program that provides reinvestment payments to projects in excess of $20 million or with equipment upgrades in excess of $2 million. For projects below those thresholds, South Dakota also offers a grant for new or expanded facilities.
Minnesota offers a Growth Acceleration Program for manufacturers that have 100 employees or less and offers grants up to $50,000. In addition, Minnesota also offers a capital equipment sales tax exemption for manufacturers.
Not to be outdone, Wisconsin has a manufacturing tax credit that can offset 7.5% of eligible income from production activities. As of 2016, the benefits of this tax credit resulted in a corporate tax rate of 0.4%.
Financing programs through banks can also create a mutually beneficial and perfect partnership between banks and manufacturing companies. Specifically, banks can help manufacturers mitigate the biggest risk of automation in the short term. And in the long term, automation can save manufacturers money through increased production, less waste, as well as decreased operating and labor costs.
Automation as a way to attract and retain talent
For many manufacturers, a good solution is one where they do not have to sacrifice their production capacity while waiting for training centers or government policies to increase the number of skilled workers. As manufacturers continue to grow and move to the next level of production, automation seems like the obvious solution that will address the prevailing labor shortage.
Automation can also solve the image problem that manufacturing is dirty and low-skilled, which is a key reason why many young Americans do not consider manufacturing jobs a desirable career choice.
Although automation is often blamed for replacing workers, it has also provided an opportunity to shape the future perception of manufacturing jobs. For companies who adopt automation, being “high-tech” can be a great selling-point to recruit and retain talent. This is because automation allows workers to direct their productivity towards high-skills activities such as software management, analytics-driven operation, and specialized electrical and mechanical skills. These value-add activities will provide an opportunity for workers to develop marketable skills and open the door to career advancement beyond the shop floor.
With the adoption of automation, manufacturing leaders will be a good position to create a more advanced and safer shop floor as well as more high-skilled jobs that will drive stronger wage growth for manufacturing workers. Communicating that automation leads to an innovative and upwardly mobile career path is a way to market and position manufacturing jobs as a viable top career choice.
As manufacturers embrace automation, up-skilling current labor becomes even more critical. If manufacturers work together to create economies of scale, they could potentially re-skill 45% of low-skilled workers at risk of being replaced by automation. If government agencies join this effort, they could re-skill as many as 77% of at-risk workers . Showing current and prospective workers that the industry is committed to training, building talent and providing job security to handle the demands of automation is also important to changing the perception of manufacturing.
Changing landscape requires leaders to be forward thinkers
In the coming years, technology, programming and critical thinking skills will become even more critical on the plant floor. And early adopters of automation will be at a competitive advantage, influencing the types of labor skills needed.
Due to the benefits of automation, it may be one of the most viable solutions available to us today. As with any investment, it requires careful financial planning. My advice to you - find a good banker who thoroughly understands the industry to take that journey with you.
Change does not come easy and sometimes the way forward requires some growing pain. But forward-thinking manufacturers are in a prime position to lead the charge. And a strategic banking partner can help you make that leap into automation and shape the future of manufacturing jobs.
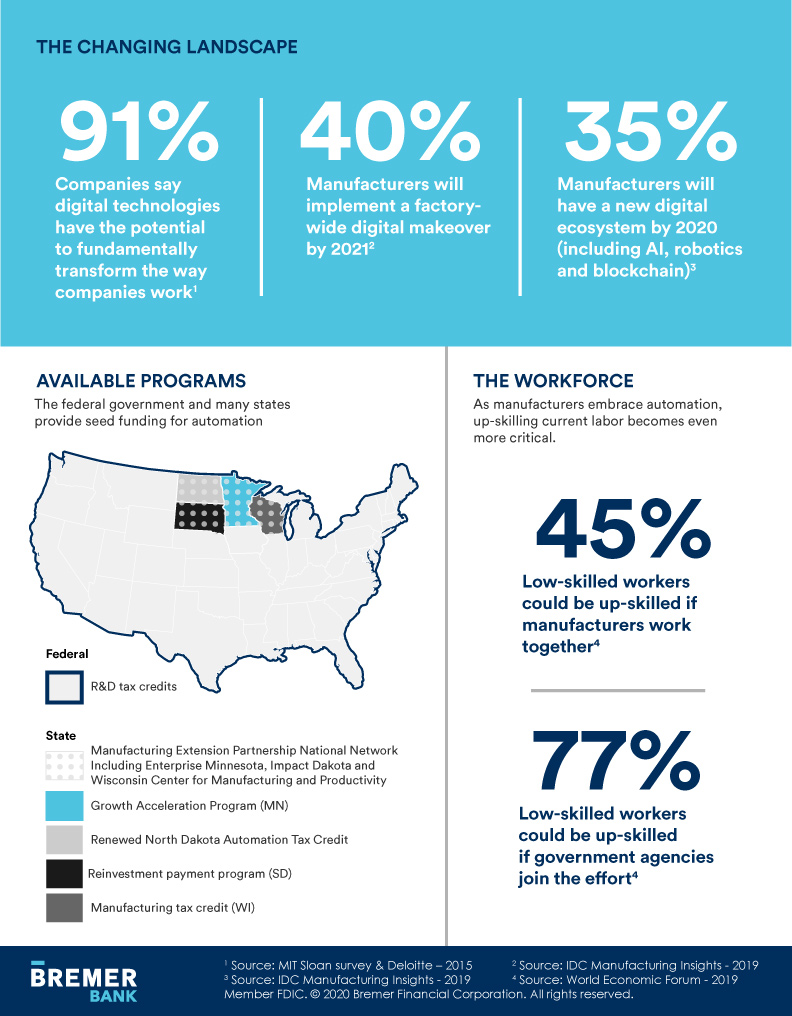